Developing Sustainable Operations at Drayton: Building a Smart Factory
Building a Smart Factory
With a goal to develop sustainable operations, Drayton are building a smart factory which will reduce their scope 1 and 2 emissions through the smart management of energy.
At Drayton, as part of their roadmap to becoming a Net Zero site by 2025, next month they will enter Phase 1 of their smart factory installation in Plymouth, UK. Using Schneider Electric’s EcoStruxure™ platform, they will transform their energy management and automation to allow real-time tracking and optimisation of energy usage across their site.
This project represents a huge step forward in reducing their carbon footprint and perfectly complements Drayton’s switch to a 100% renewable energy provider at the start of 2019.
What is EcoStruxure™?
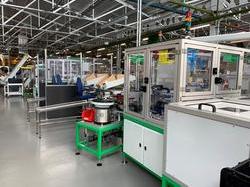
Schneider Electric, a leading provider of energy and building management systems, developed EcoStruxure™ to be a digital backbone that connects operation technology like factory machinery, with information technology that both collects and delivers performance data and utilises smart solutions to optimise performance.
Drayton’s path to a smart factory
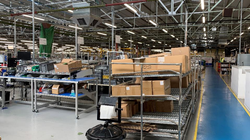
- Complete their Carbon Survey energy efficiency audit – with these results the impact of EcoStruxure™ can be reliably monitored to assess their real-time energy savings.
- Collection of available data from machinery and mapping of existing manufacturing and software solution.
- Cost analysis and final approval
- Installation of connected network of meters and loggers across all our site’s electricity, gas and water sources.
- Implementation of edge controls and software, including Wiser for heating, EcoStruxure™ PME for electrical power and Node-RED and Machine Advisor for factory machinery.
- Installation of the integrated Andon alert system plus digital information boards to enhance employees’ health and safety, a key element of their holistic approach to sustainability.
- Integration of analytics and services including Resource Advisor, Power Advisor, and utility metering – this will perform checks on all devices every 5 minutes.
- Completion of EcoStruxure™ commissioning with the support of Schneider Electric field experts.
Drayton’s Project Manager for Sustainability, Debie Robinson, describes Drayton’s latest project in their journey to more sustainable operations:
EcoStruxure™ is an innovative plug and play SMART system that will improve our manufacturing plant performance with real time data analytics. By monitoring real-time consumption, we can identify peaks at equipment and plant level, which in turn will allow us to make adjustments for efficiency savings.
What are the benefits of a smart factory solution like EcoStruxure™?
- Drayton anticipate savings of around 10%* in their electrical, gas and water consumption, a major step forward in their goal to become a Net Zero site by 2025.
- Real-time data analytics means reactive energy efficiency optimisation, preventing wastage and saving money.
- Allows preventative maintenance.
- Enhances communication of system performance to employees and management teams via digitisation.
- Optimisation of working conditions for staff, including heating, lighting, air conditioning and water.
- Peaks in trends are easily identified and rectified.
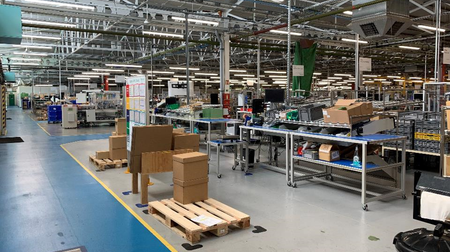
*Based on consumption savings achieved by implantation of EcoStruxure™ in a similar Schneider Electric site in Flint, UK.
Drayton and EcoStruxure™
We look forward to updating you with Drayton’s experience of implementing and making best use of the EcoStruxure™ platform at their Plymouth site and the improvements to efficiency and monitoring this infrastructure will bring to their operations.
Read more about Sustainability at Drayton.
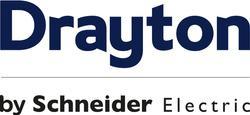
Climate commitment: Net Zero Site 2025 Climate Accreditations: ![]()
|